Full Metal Jacket
Built with 11km of copper, and winner of TIME Best Inventions.
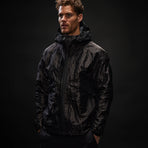
- Jacket built with over 11km of copper
- Highly waterproof, windproof and breathable
- 7 pockets and metal detailing
Hailed by WIRED as “the virus-killing coat of the future,” and winner of TIME Best Inventions, every Full Metal Jacket is built from 11 kilometres of copper.
Copper is one of the most advanced materials in our solar system. Thrown out of supernovas billions of years ago, it became central to the rise of civilisation, creating tools and sterilising water, before enabling modern day communication, transport, and electrical power. Now, as we look for materials that offer us resistance to disease on Earth and up in space, and a base on which to build intelligent clothing, copper is set to be at the centre of innovation again. Its ability to conduct heat and power while killing bacteria and viruses make it a potential first building block for the future of clothing.
To turn the Full Metal Jacket into high-performance, everyday gear here on Earth today, the copper strands in every jacket are measured by lasers to keep them soft and malleable. The jacket is engineered with an advanced waterproof and breathable membrane that can open and close to respond to different weather conditions. It comes with giant pockets, a fleece-lined neck… and it’s also cured for 6 days.
Technical Details

Winner of TIME Best Inventions, the Full Metal Jacket was hailed by WIRED as “the virus-killing coat of the future.”
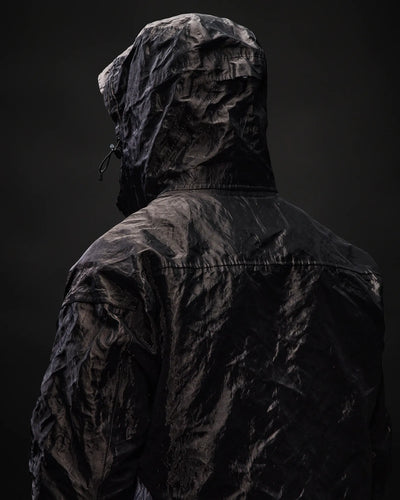
Viruses and bacteria can’t live on copper
Disease resistant clothing will become a requirement in the future, which is why we’re starting to work with copper now. It’s biostatic, so bacteria and other life forms can’t grow on it. It also has exceptional antimicrobial properties which means bacteria and viruses die when they make contact with it. The copper releases electrically charged ions which first make it difficult for a microbe to breathe, before punching holes in its outer membrane, moving in and completely wiping out its DNA, preventing it from developing any future resistance.
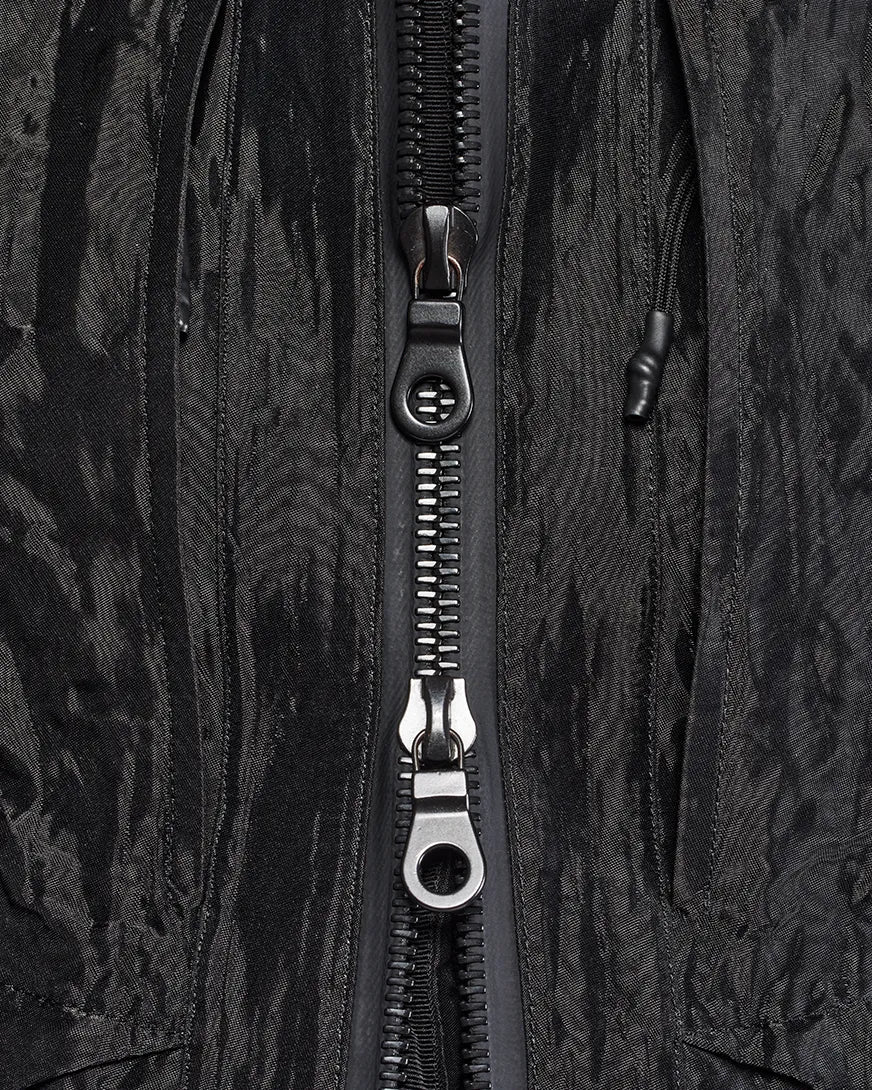
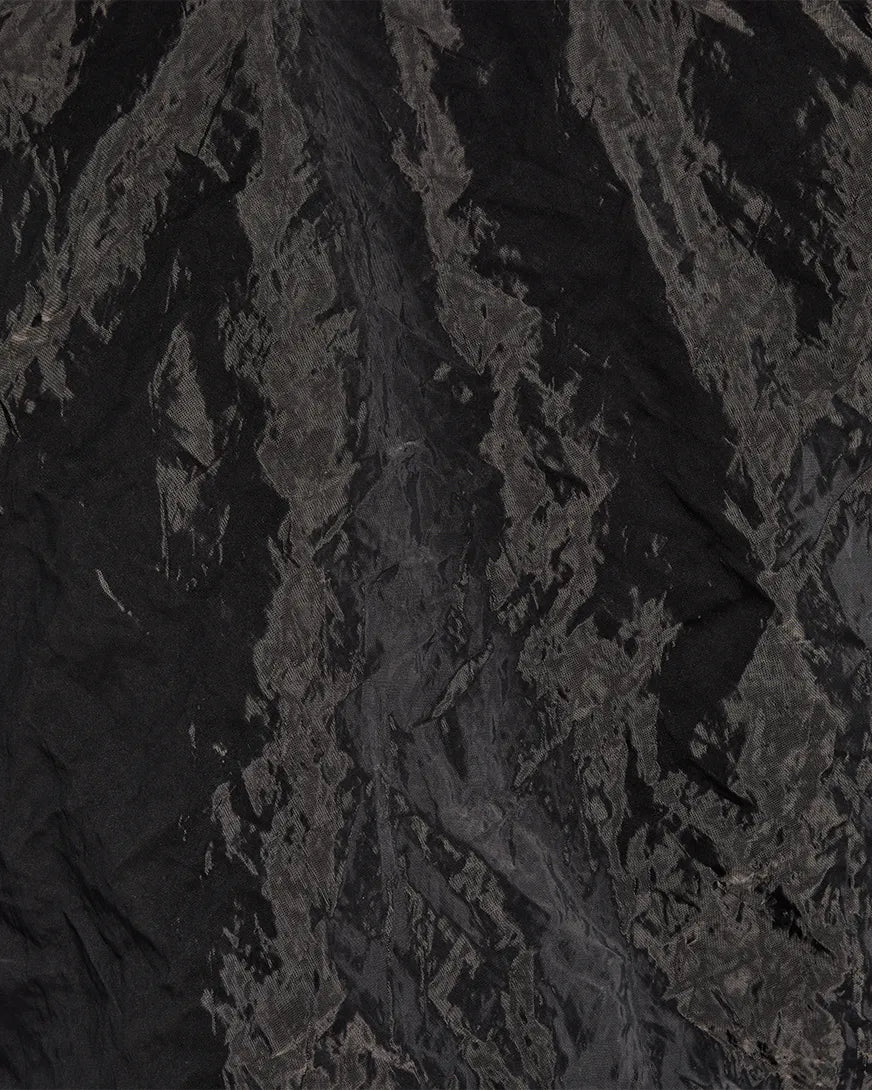
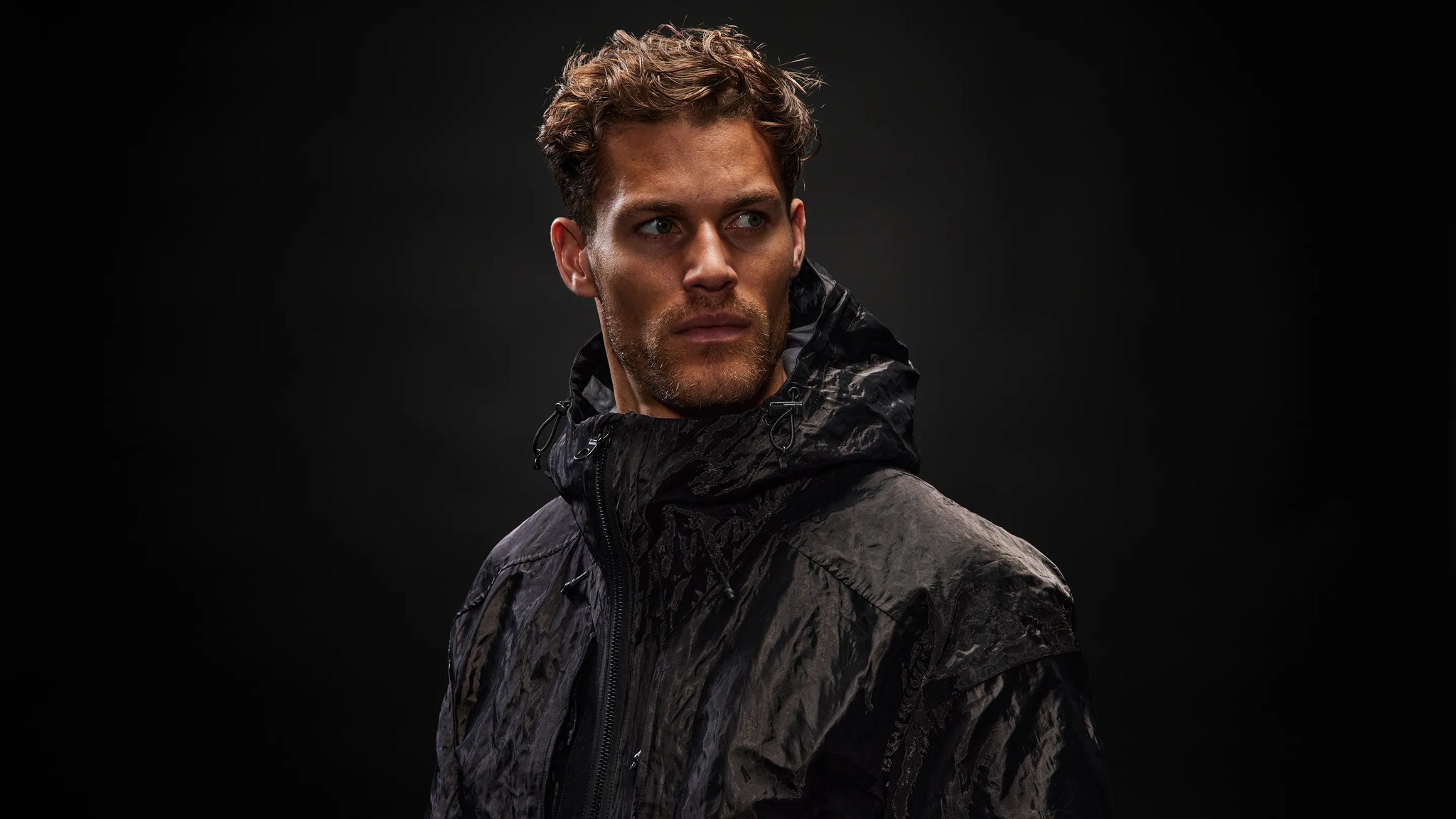
Copper was used to create the earliest recorded medical tools in ancient Egypt, and NASA are now using it to develop new medical tools for space missions.


Copper’s atomic structure helps us turn it into a jacket
There’s a reason this is the first jacket to be built mostly from metal – and that’s because metal is designed to be strong, not malleable. But copper is different. Its atoms are arranged in something called a ‘face-centred cubic crystal structure,’ which makes it extremely strong but also malleable at the same time. And this is what allows us to create a three-layered jacket that combines a soft inner layer, a high performance waterproof membrane that opens and closes in the heat, and an outer layer built from lacquered copper yarn.
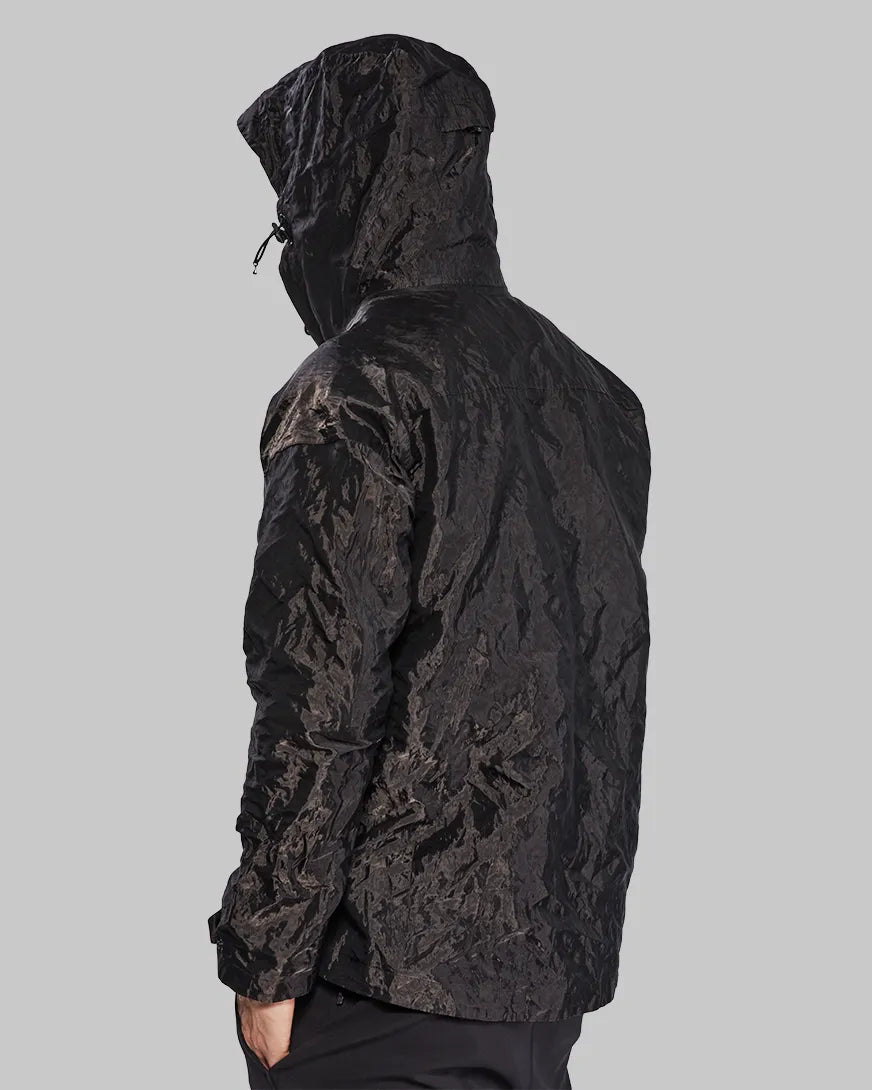
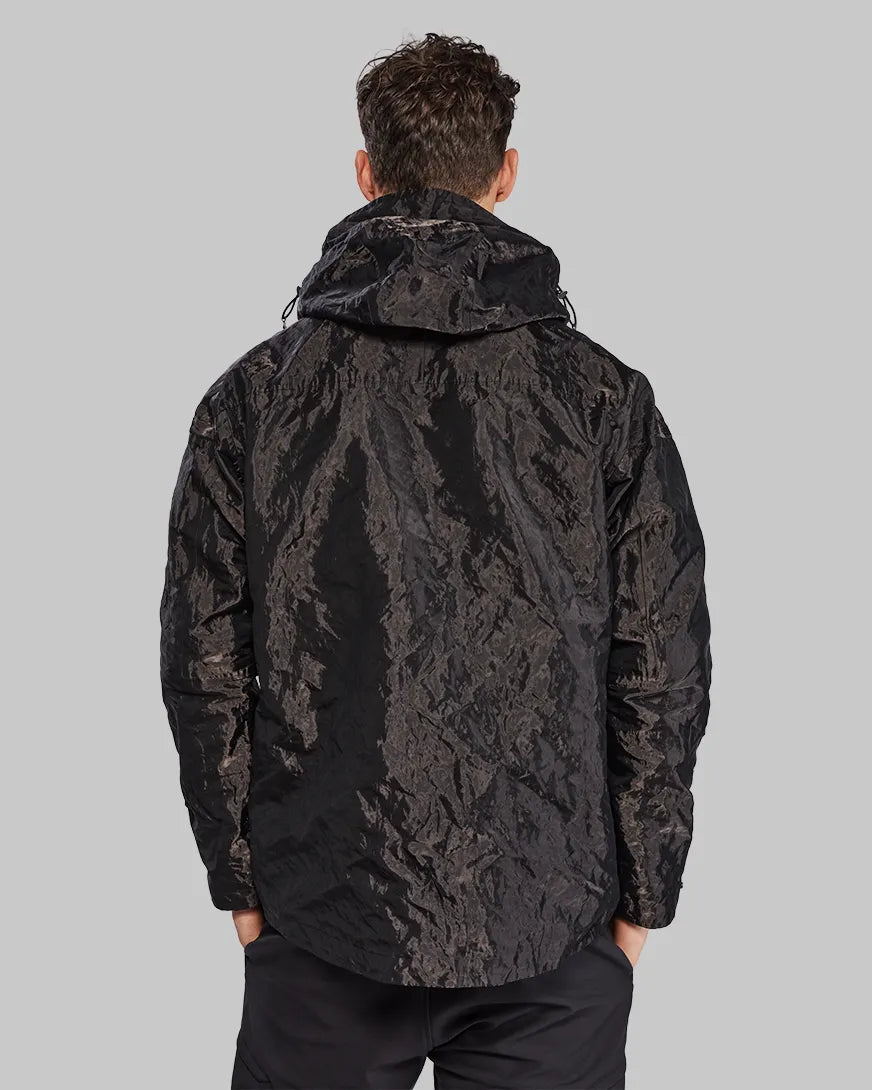

Every jacket used to be an interstellar cloud
Billions of years ago, the copper in every Full Metal Jacket was formed in the cores of massive stars alongside other heavy elements like iron and magnesium in a process known as stellar nucleosynthesis. But as these stars expanded into supergiants, they ran out of hydrogen, started dying, collapsed in colossal explosions known as supernovas, and sprayed the universe with interstellar clouds that went on to form planets like Earth. And that’s why you’ll find copper in Earth’s crust today.
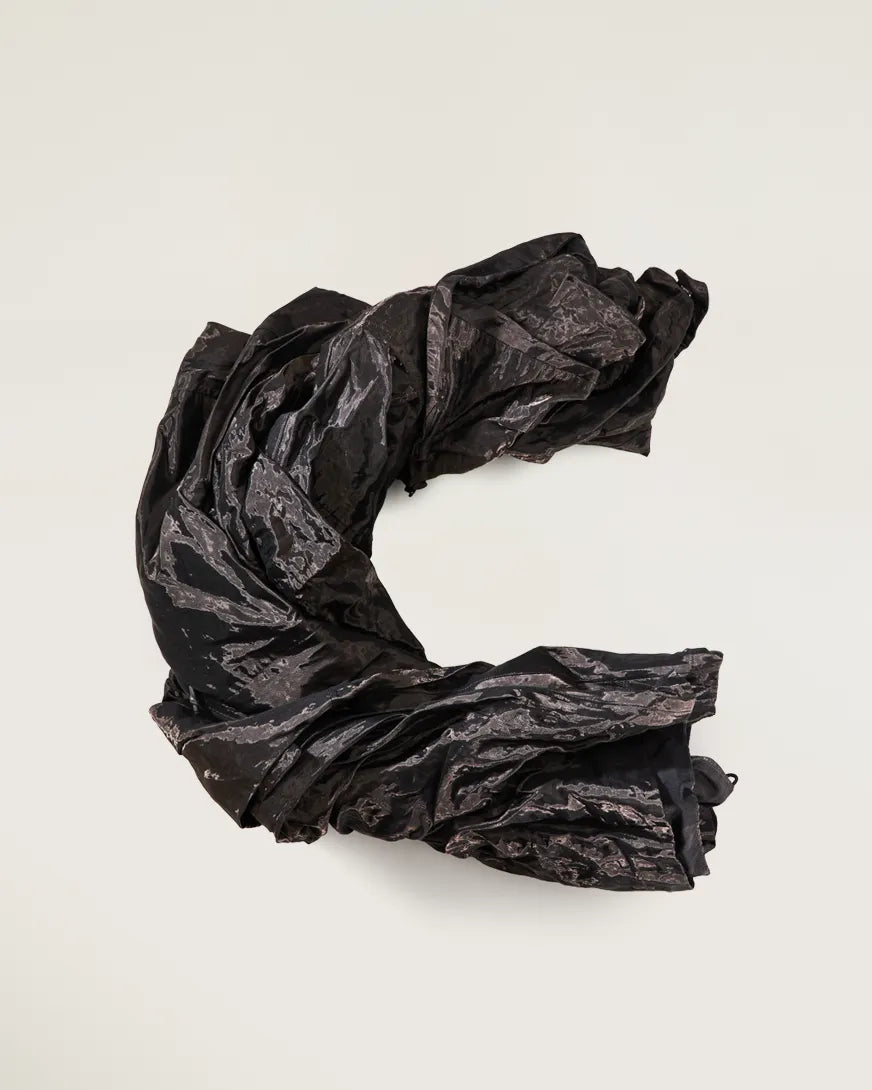
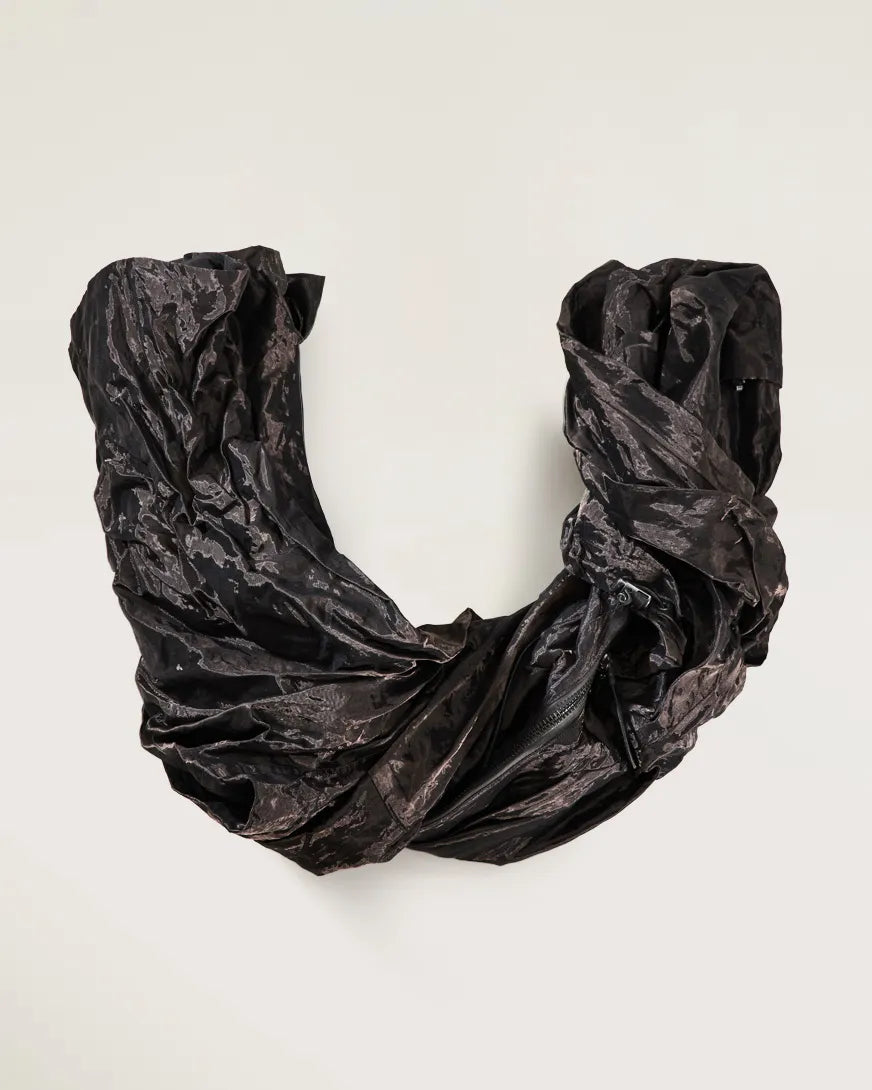
Billions of years ago, the copper in the Full Metal Jacket was floating around in an interstellar cloud.


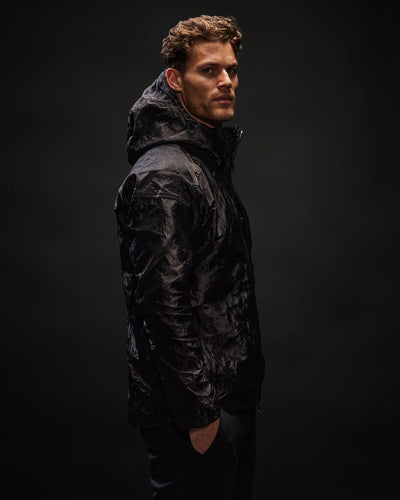
The middle layer keeps out the rain and wind
To turn the Full Metal Jacket into a high performance, highly waterproof and highly breathable piece of gear, the copper layer is laminated with an advanced waterproof and breathable membrane called c_change®. Instead of remaining static, the membrane can open and close to respond to different weather conditions as they happen, while remaining permanently waterproof and windproof.
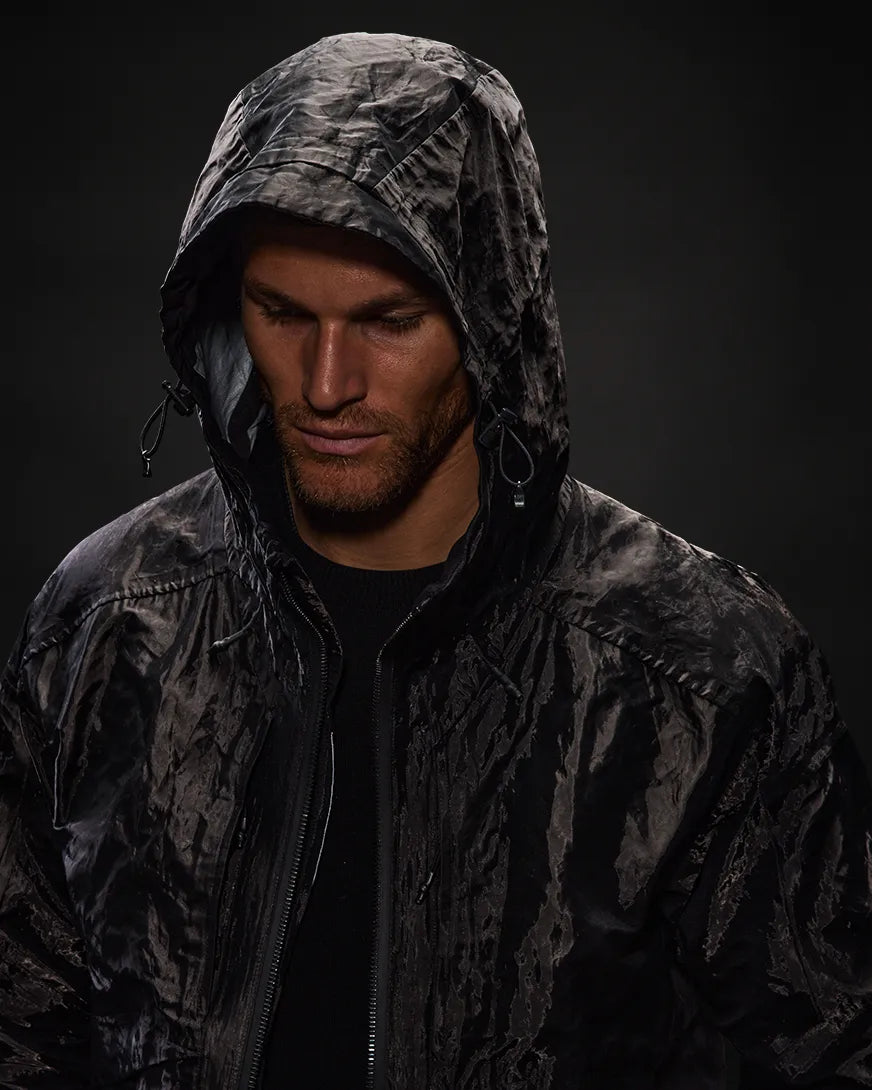
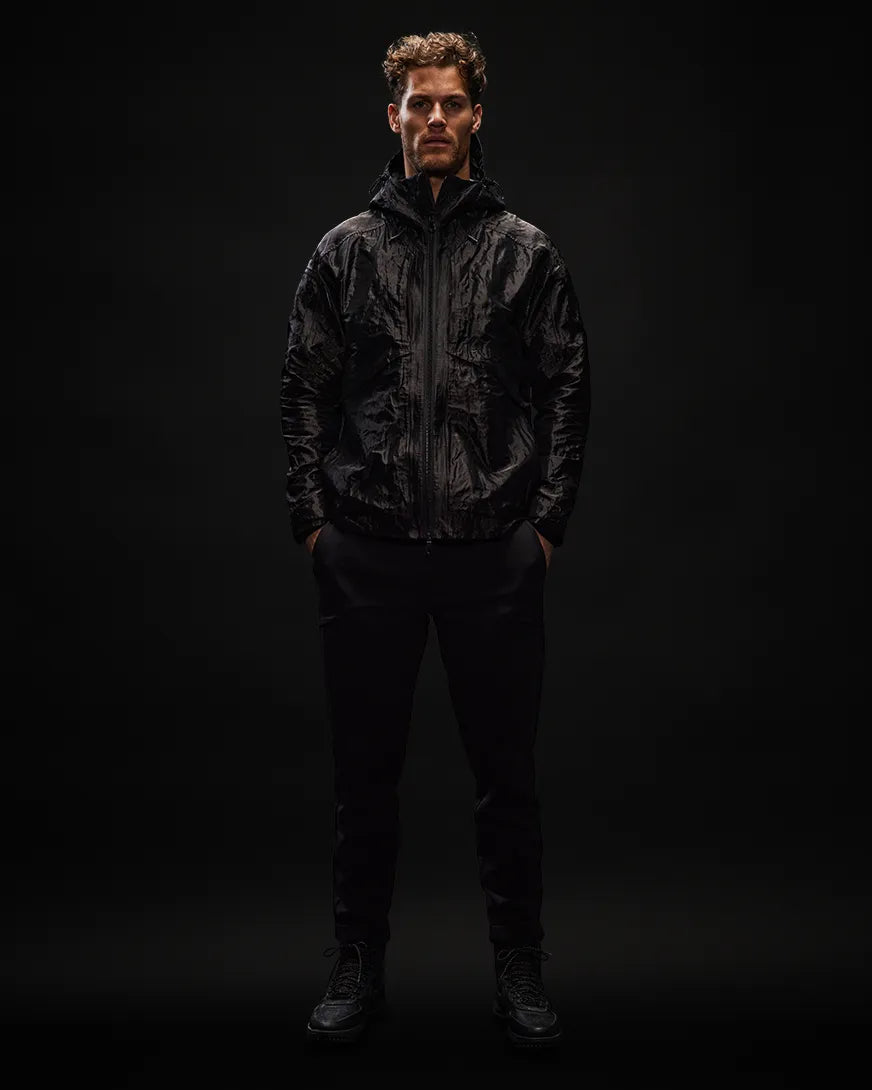
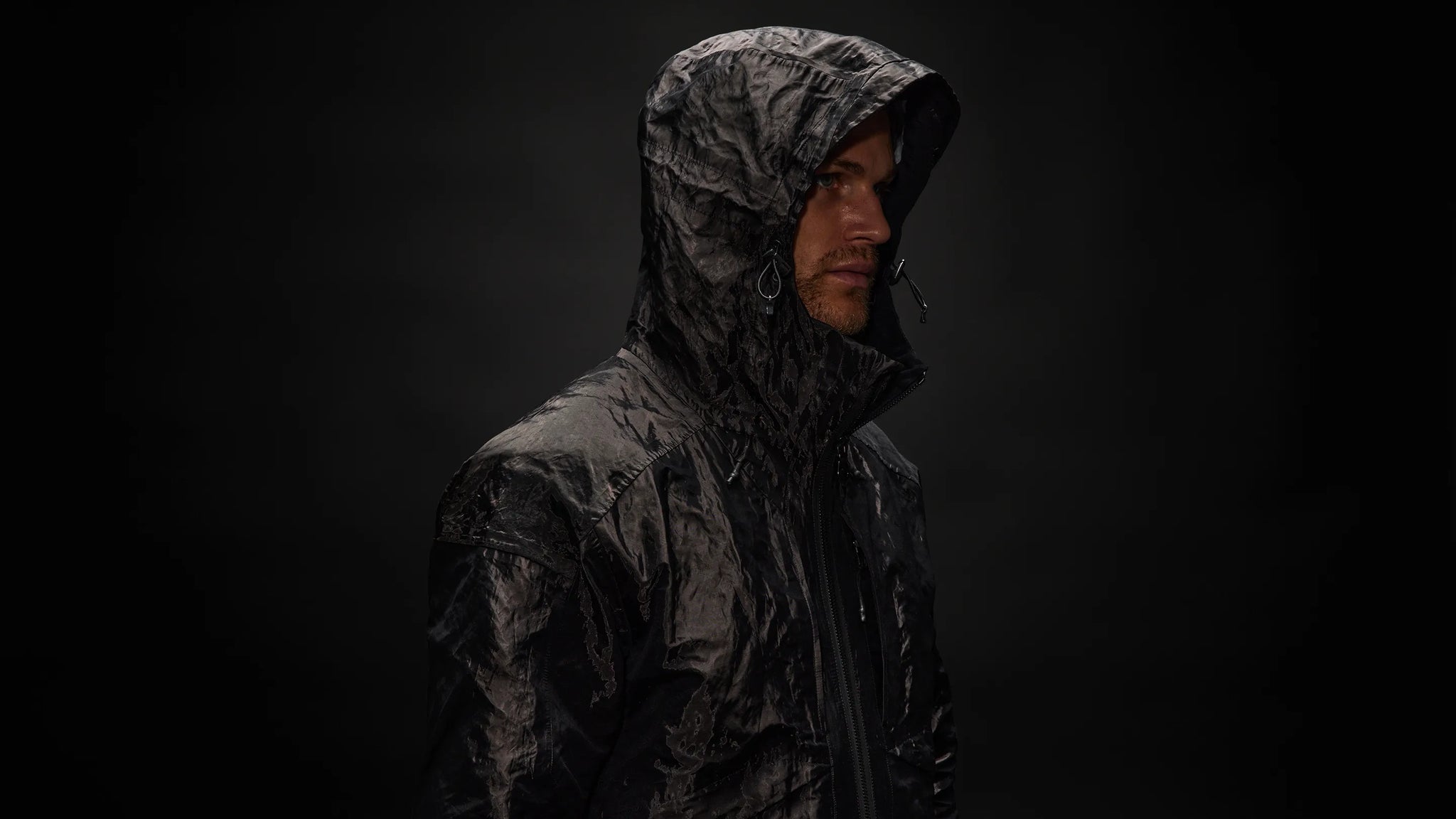

Every Full Metal Jacket is built from 11 kilometres of copper – enough to stretch from one side of NYC to the other.

The inside is built for comfort
Once the metal face fabric and advanced membrane have been bonded together, a smooth backing is added on the inside of the jacket to make it soft. The high front collar comes with a fleece-lined chinguard, and the side pockets are fleece-lined too. The hood and hem both come with elasticated drawcord adjusters. The cuffs fasten tight with metal snap fasteners. And every panel is stitched then bonded for waterproofness.
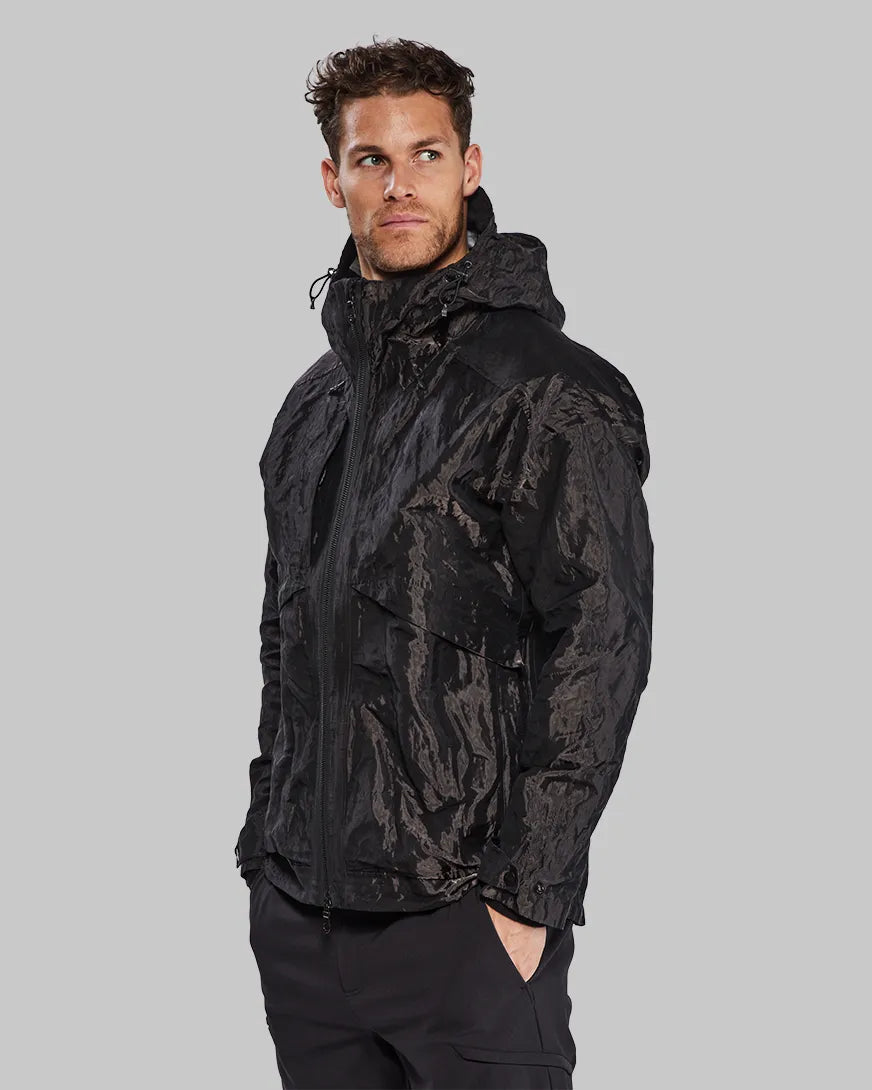
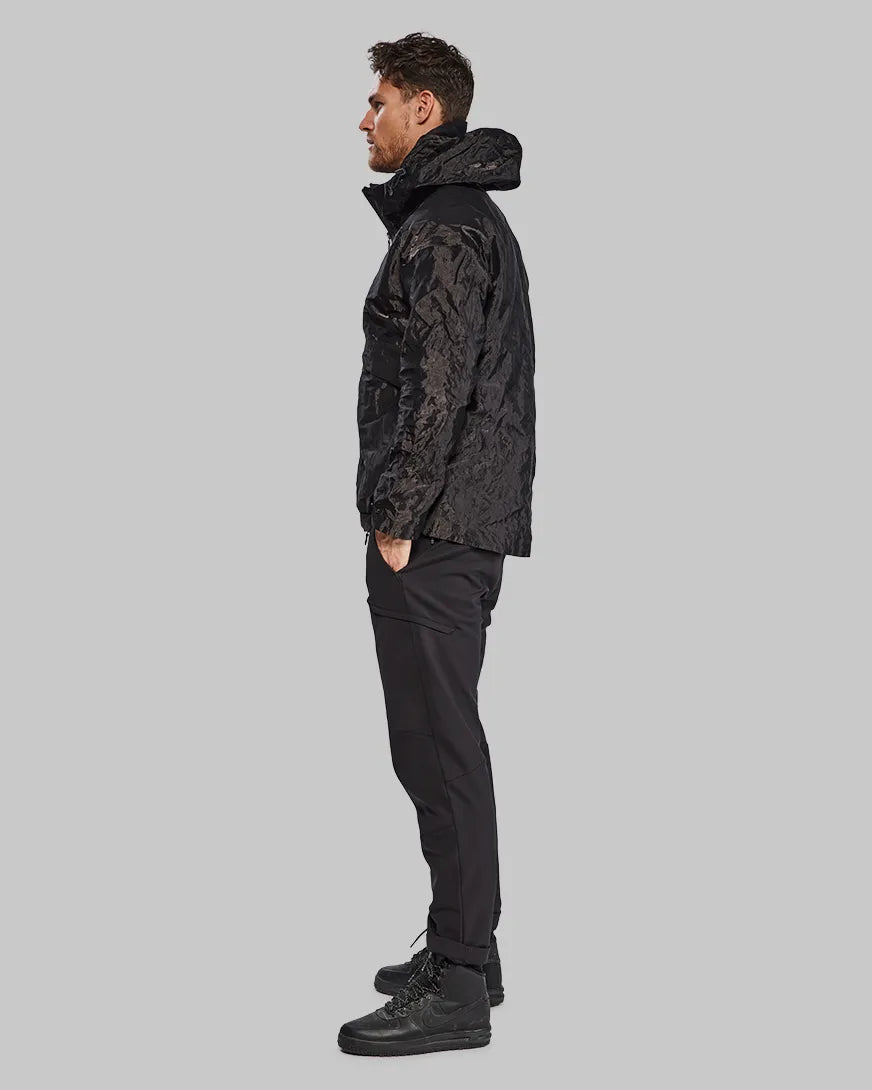


As we look for materials that offer us resistance to disease on Earth and up in space, copper is set to be at the centre of innovation again.

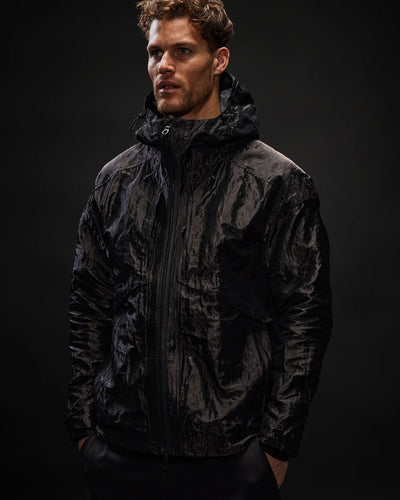
Now NASA is experimenting with copper medical devices
4,000 years after the Egyptians, NASA is exploring the use of 3D-printed copper medical instruments on long-duration space missions. One of the issues with longer missions is that astronauts can experience an altered immune response, known as Immune System Dysregulation. It’s a condition that can leave them more susceptible to infectious diseases, which can harm their performance and in turn limit human space exploration. So NASA is now testing medical instruments built from copper for use onboard the International Space Station, to help reduce the risk of infection in space.
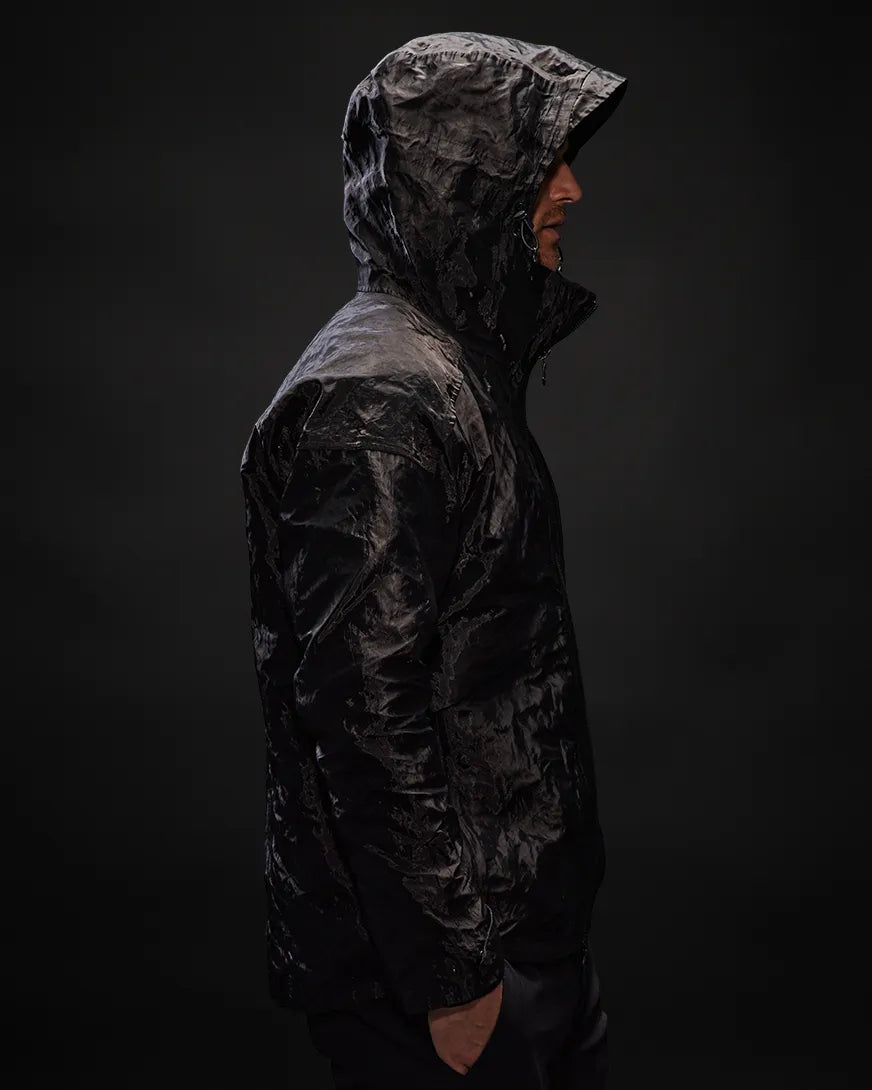
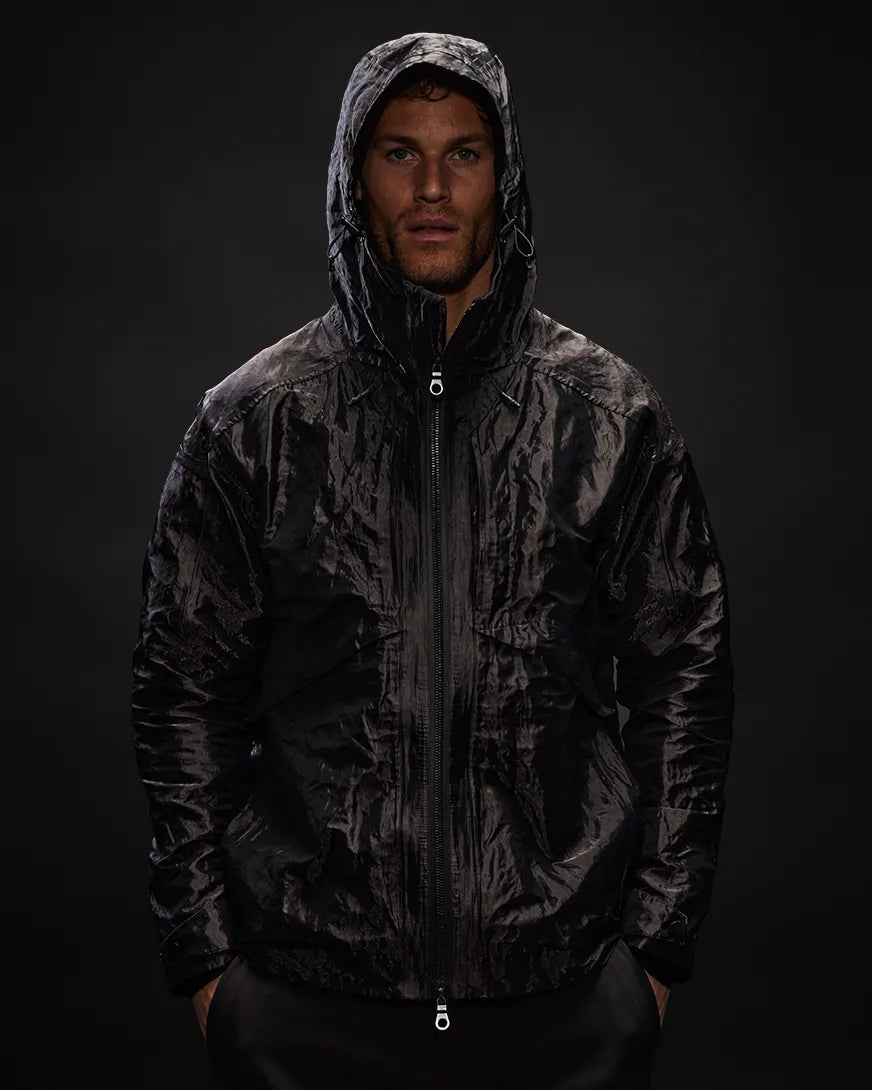
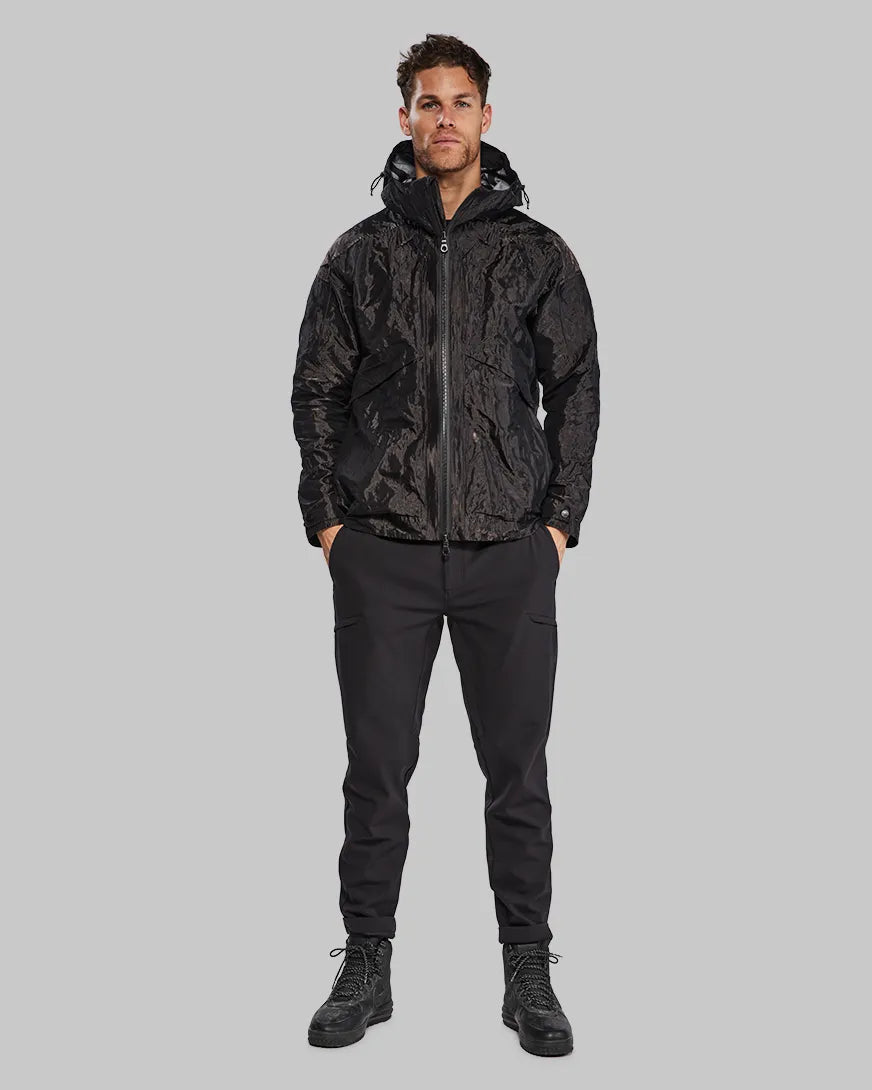
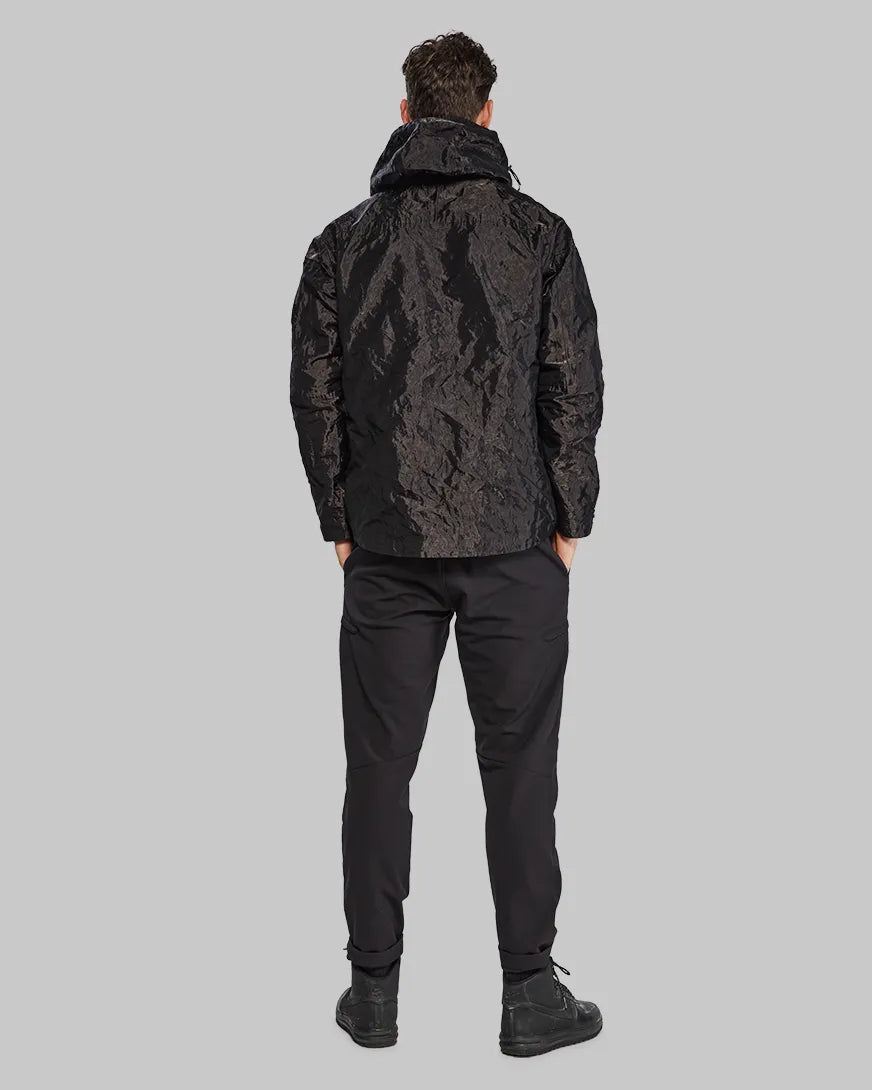
Size + Fit
The Full Metal Jacket is designed with a loose fit, with plenty of room for other layers underneath. If you prefer a closer fit, we recommend you go for the size down.
Size | XS | S | M | L | XL | XXL |
Fits chest | 83 - 90 | 91 - 98 | 99 - 106 | 107 - 114 | 115 - 122 | 123 - 130 |
Fits waist | 71 - 76 | 76 - 81 | 81 - 86 | 86 - 91 | 91 - 96 | 96 - 101 |
Size | XS | S | M | L | XL | XXL |
Fits chest | 33 - 36 | 36 - 39 | 39 - 42 | 42 - 45 | 45 - 48 | 48 - 51 |
Fits waist | 28 - 30 | 30 - 32 | 32 - 34 | 34 - 36 | 36 - 38 | 38 - 40 |